Types of welding work performed by our company:
Laser welding
Laser welding is characterized by high weld speed (4 times faster than TIG, MIG, MAG). Laser welding always results in an excellent seam. Thanks to local heating, there is no overheating or distortion. The weld seam does not need to be cleaned. It is possible to connect thin (from 0.26 mm) and thick (up to 10 mm) workpieces. Wire feed welding is also possible.
Manual arc welding (MMA, manual metallic arc)
Welding is performed using electrodes with a special coating. The welding process is conducted using direct current (DC) or alternating current (AC). When melting, the coating of the electrodes forms a gas cloud to protect the welding zone from oxidation and ensures the ingress of chemical additives to improve the properties of the metal and the stability of the electric arc. We use welding inverters from the leading global manufacturers.
This welding method allows to connect all types of metals (ferrous, non-ferrous, alloyed).
Argon infusible inert gas welding (TIG, tungsten inert gas).
Welding is performed with tungsten, carbon or graphite infusible electrodes. The inert gas used is argon, nitrogen, or mixtures of these gases, depending on the types of metals being joined. In such work, the welding seam is formed “with its own body” or with the addition of an additive. The presence of inert gases or their mixtures in the welding zone protects the weld metal and maintains the stability of the electric arc. Such work can be performed using alternating current (AC) or direct current (DC). The relatively low productivity is due to the high quality of the resulting weld. The work process is labour-intensive and requires special professional skills from the operator.
Argon arc welding is used when it is necessary to obtain critical seams that can withstand high loads and have an excellent aesthetic appearance. This includes welding of pipes, vessels and tanks of high and low pressure, equipment for the food and chemical industries, and decorative elements. This type of welding is indispensable when working with thin-walled metal structures and sheet metal (up to 6 mm), with stainless, alloy, carbon structural steel, copper, brass, titanium, magnesium, aluminum and aluminum alloys. We use argon welding equipment from leading global manufacturers.
Semi-automatic welding with a consumable continuous electrode in an inert gas (MIG) or active gas (MAG) environment.
Welding is performed using equipment from European manufacturers. A consumable electrode is a wire that melts under the impact of an electric current, which is automatically fed into the welding zone. The gas mixture composition depends on the type of material being welded. Such work is only possible using direct electric current. Automatic wire feeding into the work area (welding pool) and the ability to electronically adjust workers. The settings in the devices give excellent results.
This method of work allows to weld low-alloy and high-alloy structural steels, many types of cast iron, aluminum, copper, nickel, manganese and their alloys, and weld various types of metals.
Gas plasma welding, gas welding.
In this type of welding, metal fusion is carried out by a flame formed as a result of the combustion of oxygen mixtures of flammable gases. Welding is performed using acetylene, butane, propane, kerosene, gasoline, and hydrogen. The use of MAF (methyl acetylene fraction) is most effective, since it has a high combustion temperature (2927 C) in oxygen and good heat transfer. This compound is not as toxic as cyanogen (4500 C) and not as explosive as acetylenedinitrile (5000 C).
Due to the fact that a gas flame is used as a heat source, this type of welding does not require power.
One of the advantages of this type of work is the ability to provide gradual, controlled heating of the metal, which is convenient when working with sheet metal.
Thermo-mechanical welding, resistance welding, spot welding.
Welding is performed by heating the parts to be joined and simultaneously deforming them under pressure. Spot welding is performed using stationary spot welding machines or small welding tongs. The parts are placed between the electrodes. An electric current passed between them leads to local heating of the metal. After this, the pressure of the electrodes on the parts is increased. Crystallization of local metal melting leads to the formation of a connection point.
The work is performed using single-sided and double-sided spot welding equipment.
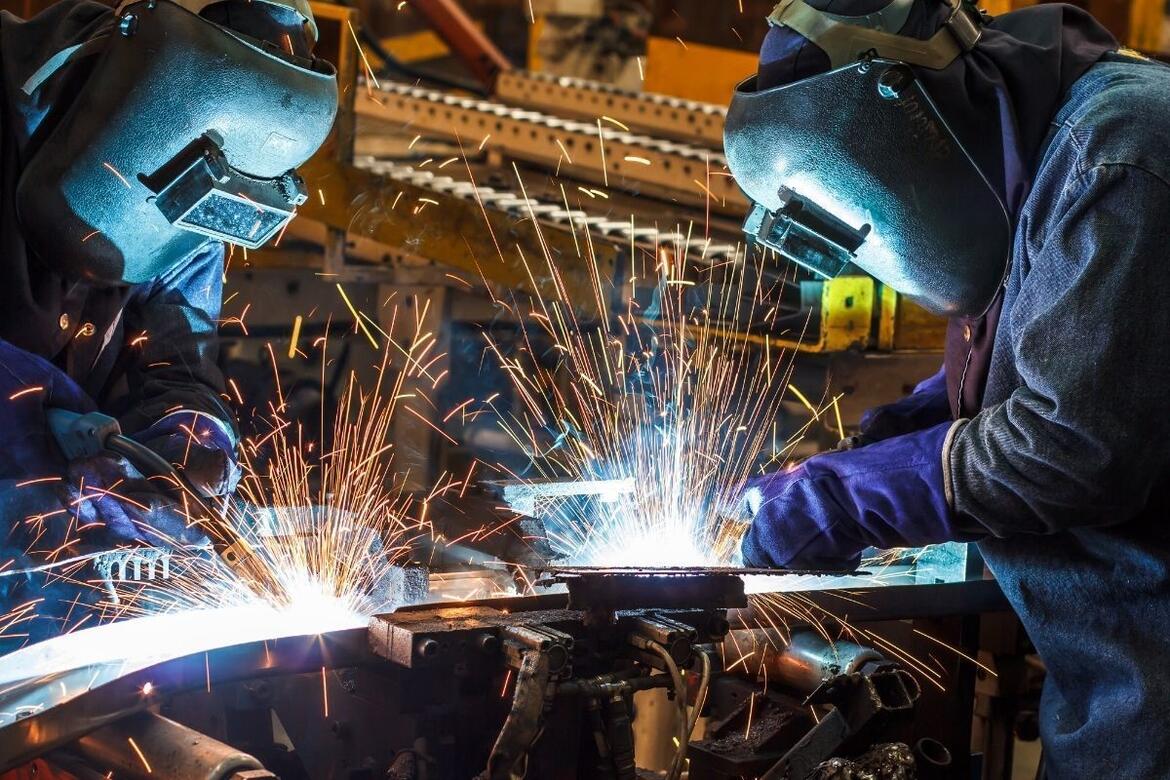
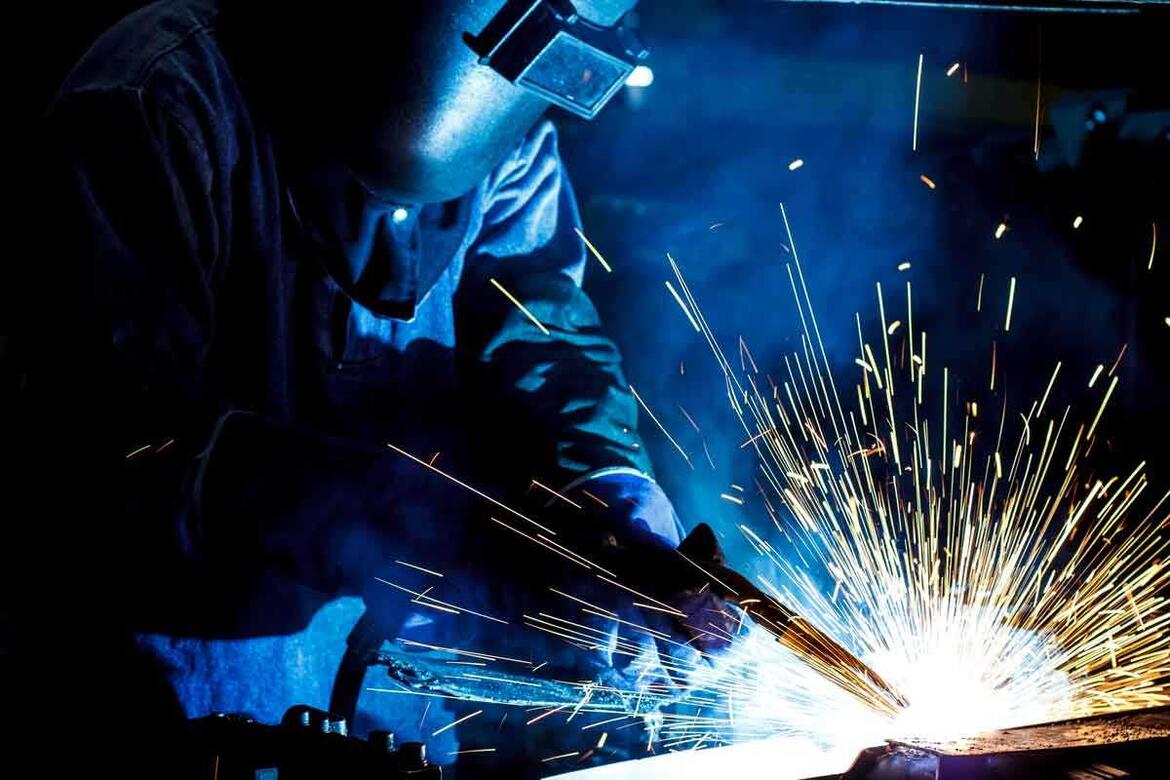
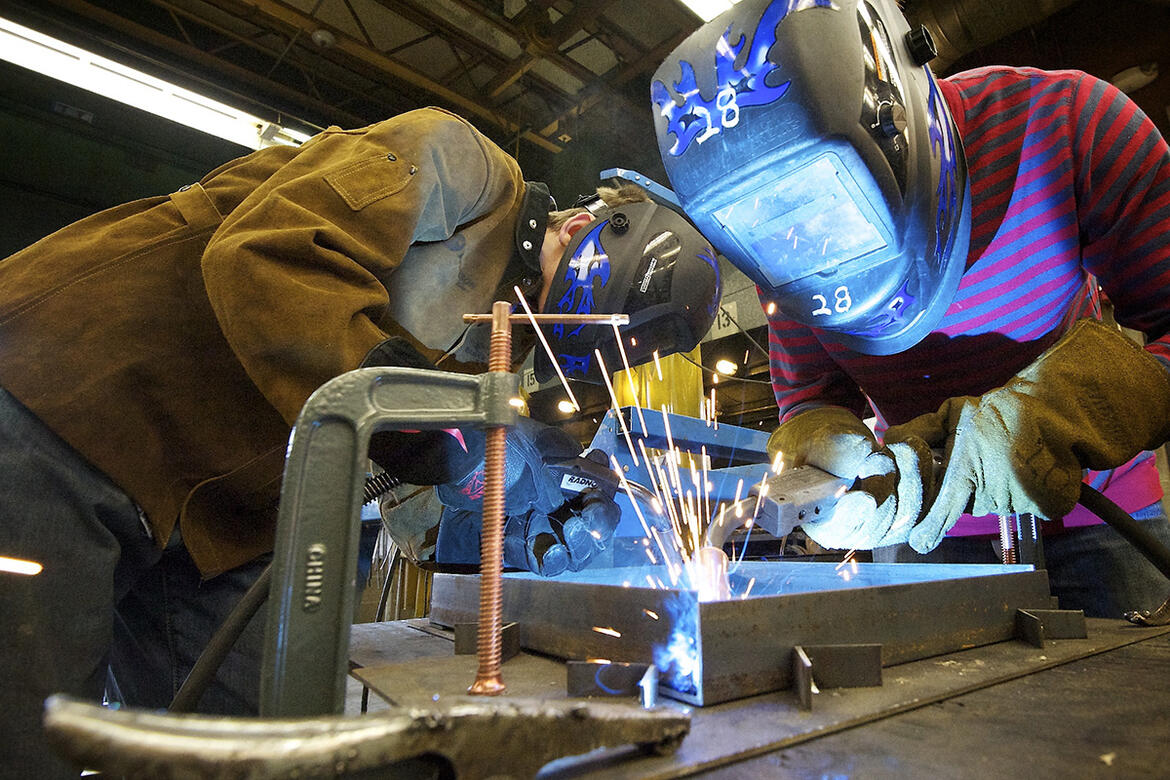