Bending is a technology for cold plastic deformation of metal. It consists of changing the shape of a metal sheet by deformation using a matrix and a movable punch. Bending makes it possible to produce complex volumetric metal products.
Free cold (V-shaped) machining of a workpiece is the most popular and common option for metal bending. Typically performed with a universal or special machining tool on a CNC hydraulic press brake. The matrix is usually placed in the lower stationary part of the press, and the punch is fixed on the movable working beam of the machine. Thus, the movable punch exerts the necessary pressure on the sheet of material being processed and, together with the stationary matrix, it produces the specified bends. In other words, the upper part of the workpiece is compressed by the action of the punch and matrix, and the lower part is pressed against the walls of the matrix mechanism and stretched, thus providing the required bending angle and radius. When bending (plastic deformation) of a workpiece, a punch is placed in the inner part of the bending angle, and a matrix is placed on the outer side of the bending angle.
The free cold forming process is typically used for metal workpieces with thickness ranging from 0.1 to 8 mm, but the exact range of possible thickness for a particular product depends on the type and grade of metal. It is also necessary to first clarify the possible bending radii.
Available bending angles for the bending equipment we use range from 24-25 0 to 170-179 0. Smaller bending angles can also be achieved. To achieve this, the matrix of the hydraulic press brake must be additionally equipped with a rolling tool. This upgrade allows the bend angle to be reduced to less than 24 degrees. Sheet metal of 0.1 to 1.5 mm thickness can be flattened.
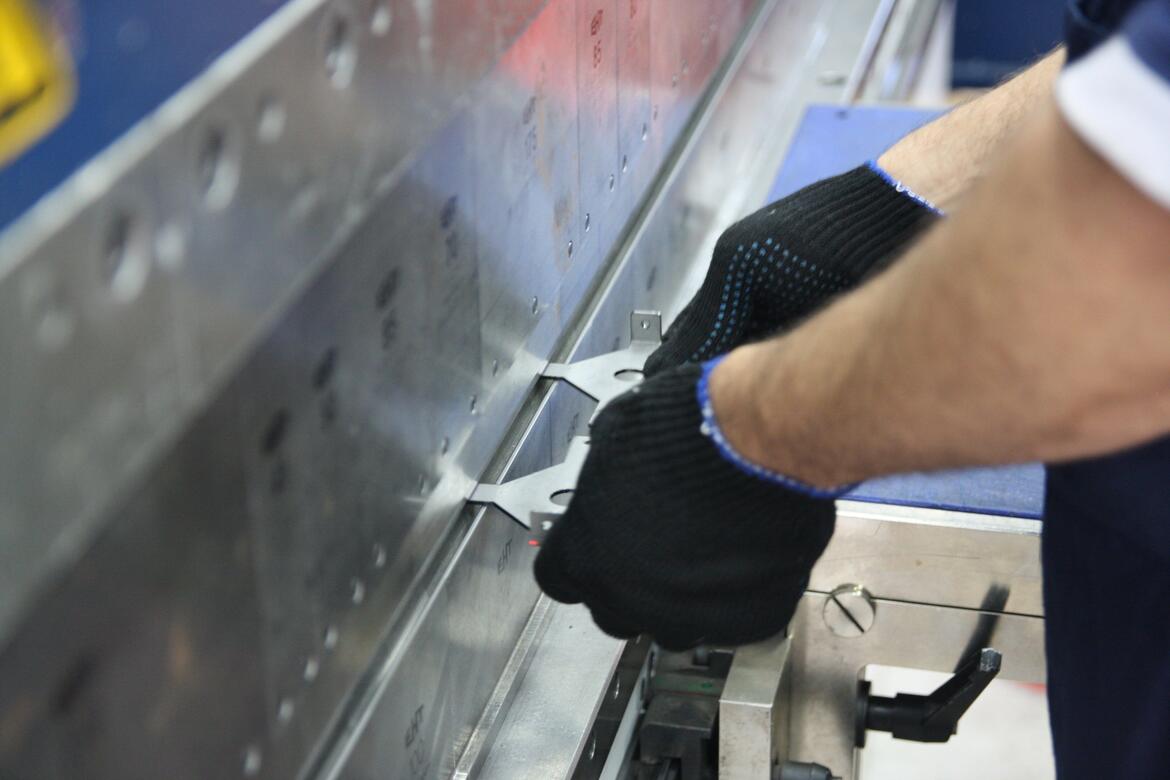
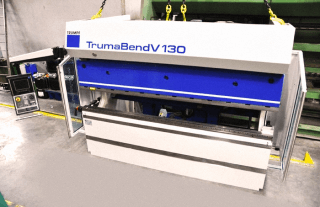
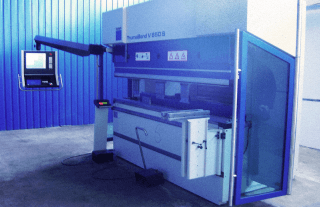
Factors affecting the quality of metal processing by cold bending technology
Total bending length when performing plastic deformation service. This factor determines the number and composition of working tools used on a hydraulic press brake. With an increase in bending length, the labour intensity of workpiece positioning in the working area of a hydraulic press brake increases significantly, and the wear of working tools noticeably accelerates, which inevitably entails an increase in the service cost.
Total weight of the part (workpiece). This important factor affects the duration of preparatory operations, the labour intensity of workpiece positioning in the working area of a hydraulic press brake, complicates intra-production logistics, and increases the overall metalworking time.
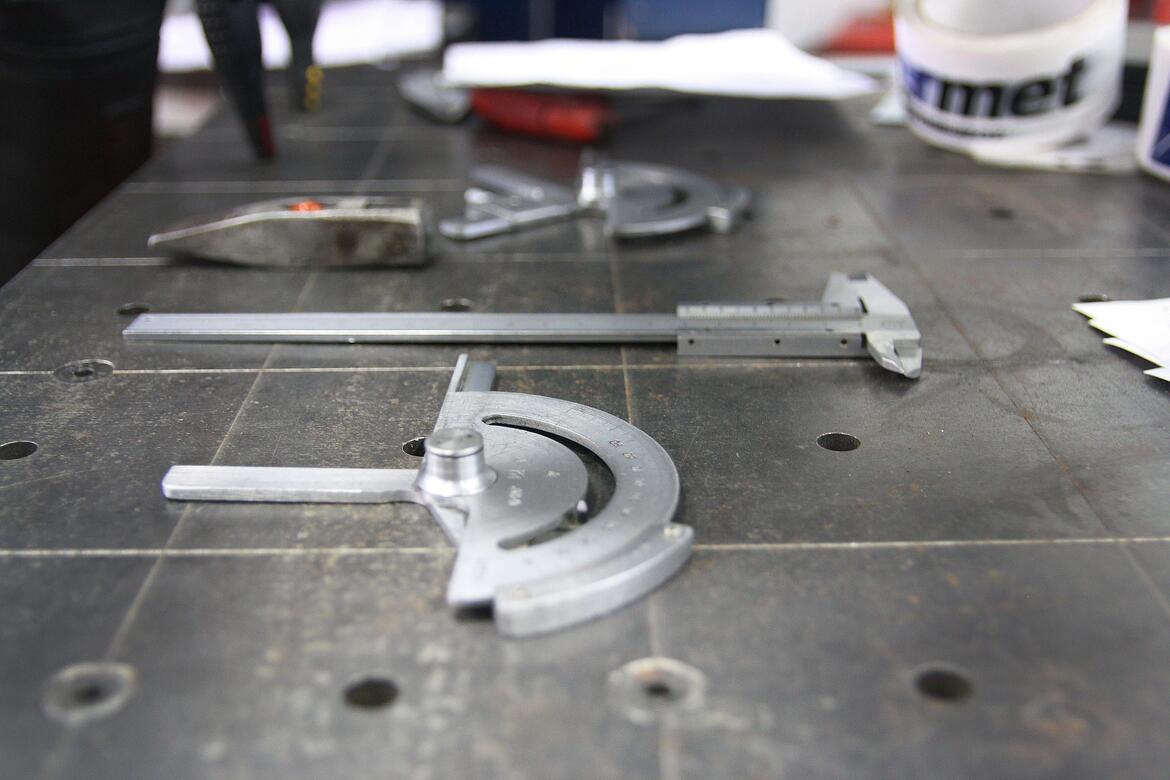
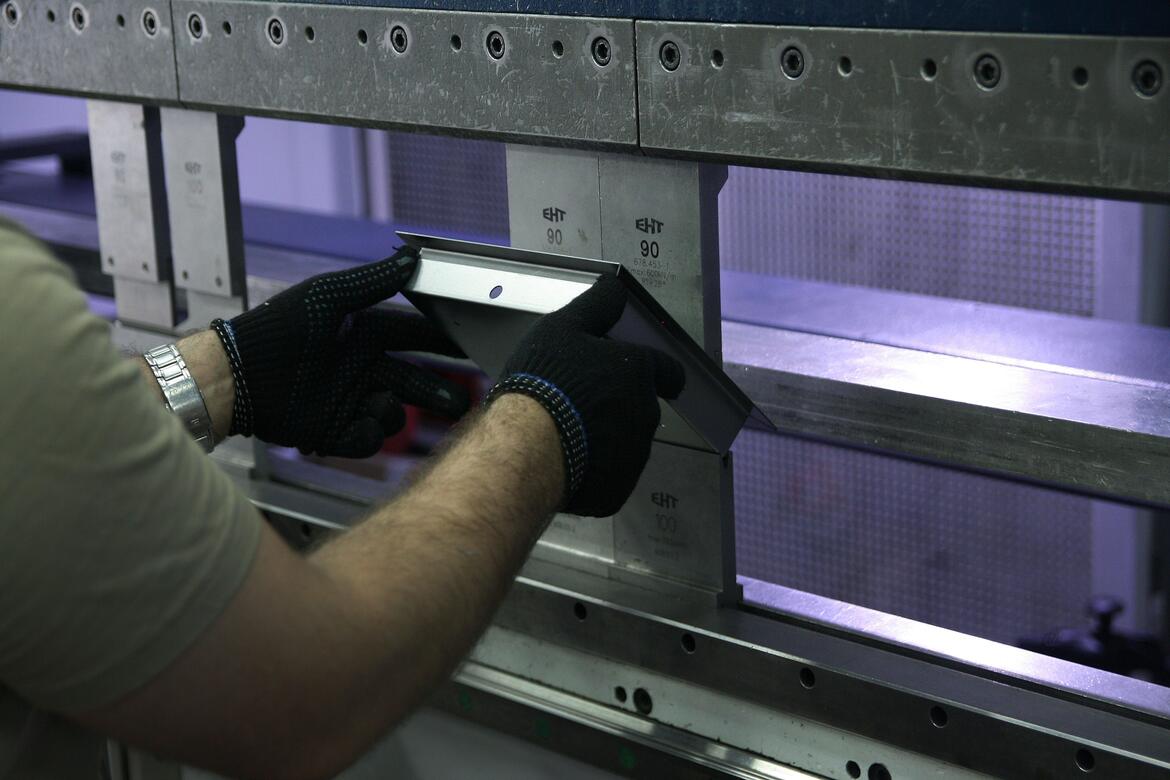
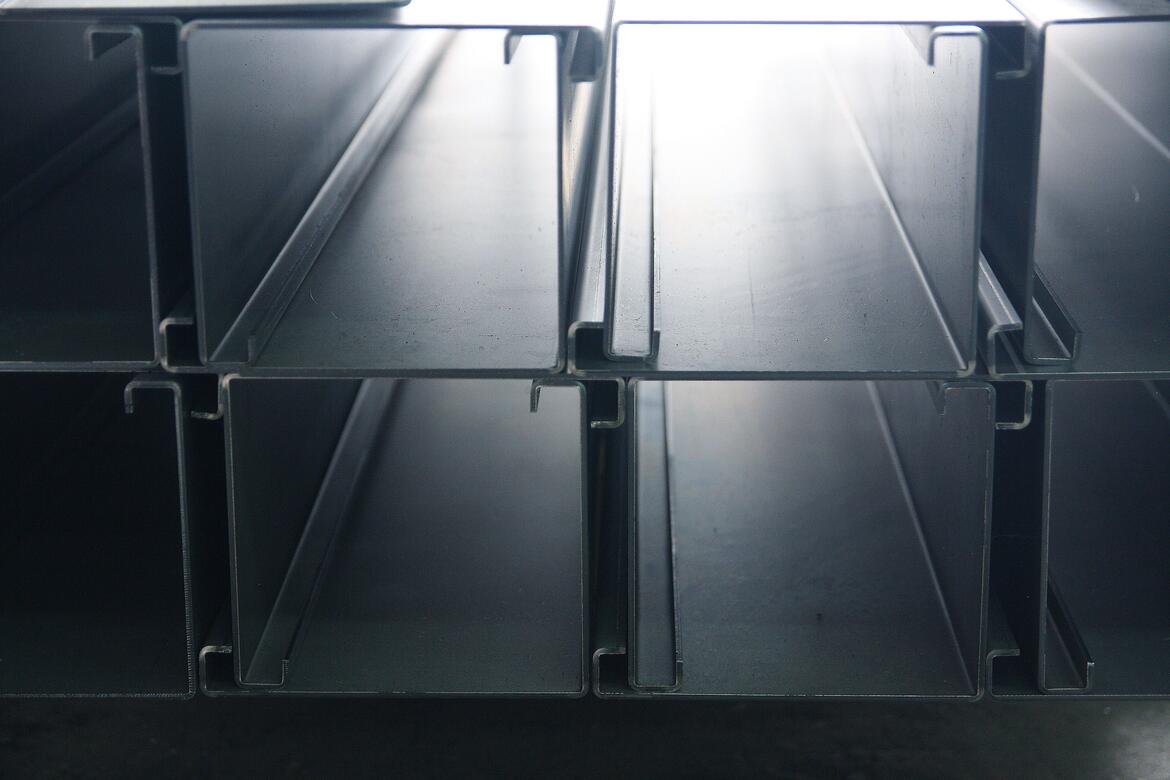